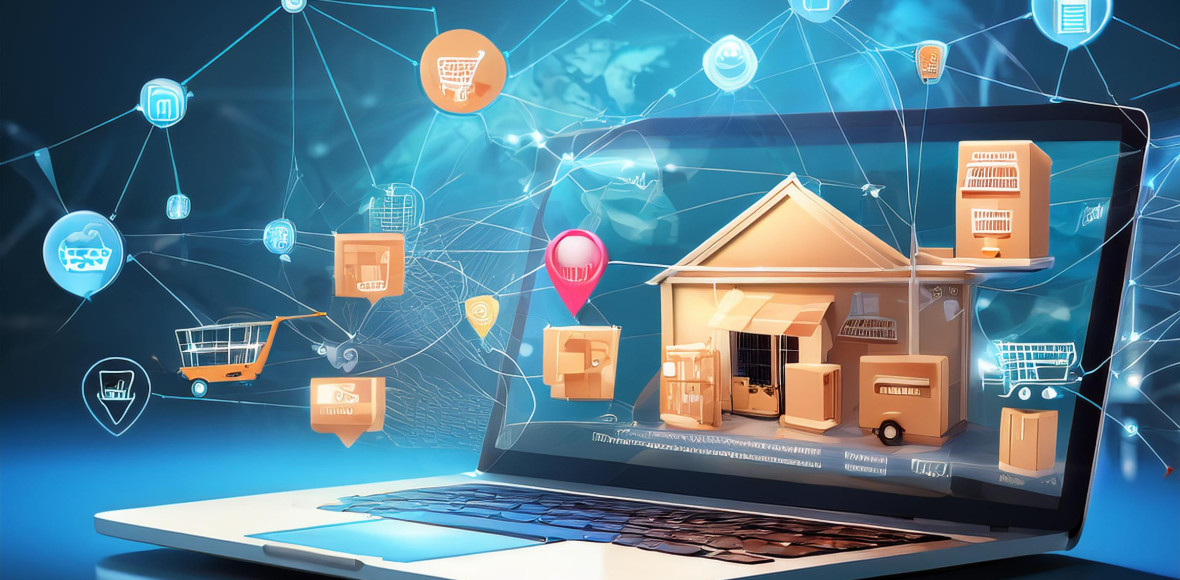
Companies today have to face unprecedented challenges when it comes to their supply chains. The global supply chain world’s been shaken up by things like COVID-19 pandemic, geopolitical tensions, labour shortages, and extreme unpredictable weather. For businesses that need their orders to flow seamlessly, these challenges outline the importance of an agile and efficient Order Management System (OMS). Modern OMS solutions besides getting orders sorted—they are built to solve super complicated and all challenges within the interconnected supply ecosystem.
Key Challenges in Current Supply Chains
- Supply and Demand Imbalances: The demand for goods can change due to seasons economic changes, and unexpected events. Poor visibility across supply networks and inventory locations can result in running out of stock or having too much making supply chain problems worse.
- Labor Shortages: Not enough warehouse and logistics workers have created problems in moving goods storing them and delivering them to customers. These shortages can slow down order processing leading to longer wait times and higher costs.
- Rising Transportation Costs: Higher fuel prices increased tariffs, and more expensive shipping rates have made it costlier to move goods between countries and regions. Companies need to manage these costs well to stay profitable.
- Increased Customer Expectations: Customers today want fast delivery and to see where their orders are in real-time. Shops and brands must meet these needs while still delivering quality and keeping costs down.
The Impact of Order Management Systems on Today’s Supply Chains
Today’s Order Management Systems (OMS) tackle these issues head-on helping companies handle disruptions while providing quick dependable service. Here’s how OMS tech can boost supply chain strength:
– End-to-End Visibility
A robust OMS works with inventory, warehouse, and shipping systems to give a single view of the whole supply chain. Companies get up-to-the-minute info on stock levels where shipments are, and order status. This clear picture allows for quick choices, like changing shipment routes or moving stock to places that need it more.
– Inventory Optimisation
OMS can use data analysis to spread inventory across locations in the best way cutting down on empty shelves and extra stock. By keeping balanced stock levels, businesses can react to demand shifts and save money.
– Automated Order Routing
Advanced OMS solutions have smart order routing features, which assign orders based on things like how close they are, what’s in stock, and how much a place can handle. This smart system means faster deliveries and lower shipping costs by picking nearby fulfilment centres or stores for orders close by.
-Flexible Fulfillment Options
An agile OMS offers various fulfilment options, including ship-from-store, curbside pickup, and dropshipping. These choices enable retailers to utilize inventory from local stores or third-party vendors, which lessens reliance on centralized warehouses and helps mitigate the effects of labor shortages and regional disruptions.
-Predictive Analytics for Demand Forecasting
OMS platforms equipped with predictive analytics assist businesses in forecasting demand by examining historical data, market trends, and external factors like seasonality or promotions. This insight allows companies to strategically position inventory in areas with high demand, reducing lead times and minimizing the risk of stockouts.
-Enhanced Customer Communication
In a time when customers seek transparency, a modern OMS can support real-time communication. Automated notifications regarding order status, estimated delivery times, and shipment tracking keep customers informed and lessen the workload on customer service teams.
-Leveraging Technology Partnerships for OMS Integration
Integrating an advanced OMS with other digital tools, such as AI-driven supply chain platforms, Internet of Things (IoT) devices, and cloud-based solutions, can significantly boost resilience. For example, IoT sensors can deliver real-time information on shipment locations and conditions (like temperature for perishable items), while AI tools can pinpoint potential bottlenecks and recommend alternative routes or fulfilment centers.
Conclusion: Adapting to Future Supply Chain Challenges
In today’s unpredictable supply chain landscape, having a flexible Order Management System is essential rather than optional. By utilising advanced OMS technology, companies can gain comprehensive visibility, optimize their inventory, and enhance their ability to adapt to disruptions while meeting increasing customer demands. As supply chain issues continue to change, businesses that focus on building a robust Order Management System will be in a stronger position to sustain operational efficiency, lower costs, and improve customer satisfaction. Investing in a modern Order Management System not only equips businesses to tackle present challenges but also lays the groundwork for a more agile and future-ready supply chain.