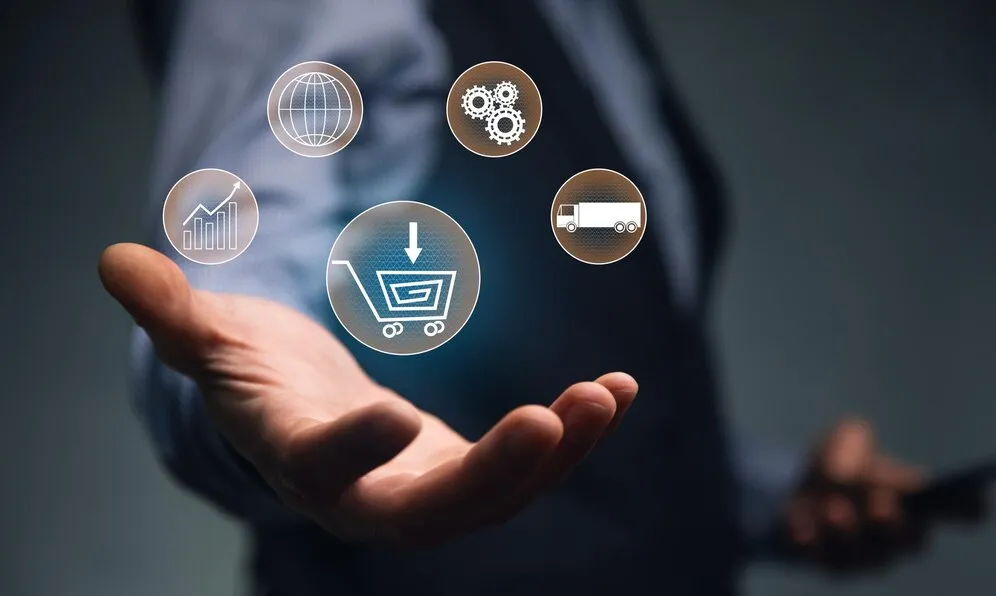
An Order Management System (OMS) is a digital tool that makes the whole order fulfilment process easier, from the time a customer places an order to the time they get it. It helps businesses handle orders well across different sales channels—online, in stores, or through other platforms. It helps to automate make key tasks, like keeping track of stock, communicating with customers, and dealing with returns.
Integrating an OMS to your business can boost order accuracy, make workflows smoother, and make customers happier. But achieving seamless order management integration isn’t always easy. Whether you’re connecting with online shopping platforms, ERP systems, warehouse management systems (WMS), or other tools, you need to plan and carry out the process. Here are seven best practices that can help ensure a seamless order management integration.
1. Set Clear Goals and Needs
To have a successful order management integration, you need to set your goals and requirements. Knowing what you want to get out of the integration is key. This could mean making orders more accurate, speeding up how you handle them, or seeing what’s happening across all your sales channels. Clearly outline what the project will cover, including which systems you want to connect and what they should do. This helps to prevent the project from growing too big and keeps everyone on the same page about what you’re trying to do.
Think about these questions:
- What’s not working well in how you handle orders now?
- Which systems do you need to integrate with the Order Management System?
- What do you hope will change after you integrate?
When you know what you want, you can tell your tech partners clearly. This means you’re less likely to face delays or have to redo work while you’re putting everything together.
2. Pick the Order Management System That Fits Your Business
Finding an OMS that matches your company’s requirements plays a key role in smooth integration. Order management platforms differ; some work better for specific industries or business types than others. As you look at some system options, think about these points:
- Growth Potential: Is the system able to handle your current order numbers and grow with your business?
- Ease of Connection: Does the system have ready-made connectors or APIs to link up with other systems?
- Flexibility: Can you tailor the system to fit your specific processes, or is it too set in its ways?
- Easy-to-Use Design: A tricky or hard-to-navigate interface can cause mistakes and slow down order handling.
By selecting an OMS that fits your business needs and is designed to connect, you can steer clear of unnecessary hurdles during setup.
3. Invest in Data Mapping and Standardisation
Getting data to flow between systems is one of the biggest hurdles in order management integration. This calls for careful data mapping and standardisation. Data mapping lines up data fields across different systems making sure that info like order details, customer data, and inventory levels transfer between platforms.
Data standardisation matters just as much, since differences in data formats (like date formats or units of measurement) can cause errors or make integration fail. Spending time to standardise data across all systems ensures the Order Management System can communicate with other platforms leading to more accurate order processing and reporting.
Good practices include:
- Doing a thorough check of your current data to spot differences.
- Making a data dictionary that spells out data fields, formats, and rules to enter data.
- Keeping data mappings current as your systems or business processes change.
4. Leverage APIs for Integration
APIs (Application Programming Interfaces) form the core of modern system connections allowing different software programs to talk and swap data. When connecting an OMS, using APIs can make the process easier, cut down on manual data input, and make sure information stays current.
Many order management platforms offer pre-built APIs that connect with common systems like e-commerce platforms WMS, and ERP. You can tailor these APIs to meet your specific requirements creating a direct communication channel between systems.
To make the most of your APIs:
- Make sure your APIs have good documentation and upkeep, with clear rules on how to transfer data between systems.
- Keep an eye on API performance and error logs to spot and fix any problems.
- Put in place security measures like authentication and encryption to keep sensitive data safe.
5. Implement Thorough Testing Procedures
Testing plays a crucial role in any integration process. It helps to spot and fix problems before the system goes live. A complete testing plan should cover all possible situations, including normal operations, edge cases, and failure modes. This makes sure that the order management integration works as expected in different conditions and that all data moves between systems.
Main testing stages include:
- Unit Testing: Checks if individual parts of the integration work as they should.
- Integration Testing: Makes sure the Order Management System talks to other systems the right way.
- User Acceptance Testing (UAT): Brings in end-users to test the system. This confirms that it meets business needs and is easy to use.
You should run tests in a controlled setting that’s as close to your actual production environment as possible. Don’t rush this step; thorough testing will save you time and help you avoid expensive mistakes later on.
6. Focus on Change Management and Training
Integrating an OMS often changes existing work processes, so your staff needs to adapt to new systems and methods. Good change management is key for a smooth switch. Talk with your team about how the integration will help how their jobs might change and give them plenty of chances to learn the new system.
Your training should fit different job roles making sure each team member knows how to use the system and any connected systems in their daily work. Think about making a training plan that includes:
- Hands-On Sessions: Real-world training that lets users work with the system in a safe setting.
- User Manuals and Documentation: In-depth guides that show how to complete common tasks in the system.
- Ongoing Support: Help desks or support teams that users can reach out to as they learn the new system.
Good training and support will cut down on pushback, lower mistakes, and help your team get the most out of the Order Management System 1.
7. Monitor Performance and Continuously Optimise
After you implement OMS and get it running smoothly, your job isn’t done. You need to keep an eye on it and make it better all the time to keep things running. Take a look at how the system is doing, keep track of important numbers like how long it takes to process orders and how often errors happen, and ask users what they think to find out what needs work.
Think about setting up screens that show you how the system is doing right now and use what you learn from them to make smart choices. Updating and improving things can help you deal with any new business needs making sure the system keeps supporting what you’re trying to do.
Conclusion
Smooth order management integration plays a key role for companies aiming to boost their order management and upgrade their overall logistics. By sticking to these seven tips—setting clear goals, picking the right Order Management System, making data uniform, using APIs, doing thorough tests, focusing on change management, and always improving—you can make sure your integration works well. This will make things run smoother, cut down on mistakes, and help your business grow.
In today’s tough market, being able to mix and manage order systems well can make a difference. It gives companies the flexibility and insights they need to do well in the tricky world of logistics.